This project is now in update mode. Check back regularly to see how things are progressing.
UW Husky Robotics
Introduction
We are a student robotics team at the University of Washington competing in the Rover Challenge Series, which includes competitions in Asia, Europe, and the Americas with teams from all over the world. Last year, we competed in the University Rover Challenge and the Canadian International Rover Challenge. To compete, we bring together a team of over 100 diverse and motivated students to design, build, and operate a sophisticated mock Mars Rover.
In our most recent competition, we placed 2nd in the world. We believe this success was from iterating on our unique rover design, improving our mechanical and control systems, and significantly optimizing our team organization, software prototyping, and manufacturing processes.
You can visit us at our website to learn more: huskyrobotics.me
The Challenge
We design all aspects of the rover ourselves and our members do most of the machining for rover parts. To remain competitive, we incorporate composite materials, machine learning, and computer vision in our rover. Joining our team is an engineering, design, and manufacturing challenge most students do not encounter in their academic careers.
Our rover is challenged with the following tasks:
- Autonomous Traversal: The rover is given coordinates to travel towards without any driver control. Obstacles such as large boulders and gullies are overcome autonomously. This year’s challenge requires completely autonomous navigation, including obstacle avoidance and object detection. Computer Vision is mandatory, as markers are only in the general area of GPS coordinates.
- Equipment Servicing: The rover completes several dexterous tasks such as turning knobs and plugging in connectors. This year, we are also expected to enter commands on a keyboard and plug in Molex connectors.
- Extreme Retrieval and Delivery: The rover is driven through rough terrain, picking up and delivering items such as tool boxes and water bottles to predetermined locations. This is an obstacle course testing durability, navigation, speed, arm precision, and carrying capacity.
- Science Cache: The rover takes measurements and drills into the soil to take samples from under 10 cm. The sample is subjected to onboard tests, then sealed and stored for off-site testing later. Success in this task is determined by our ability to analyze a soil sample with relevant sensors & tests and give a presentation of our findings to a panel of judges from the Mars Society
Your Donation
Your donation will help build our 2020 rover, Hindsight.
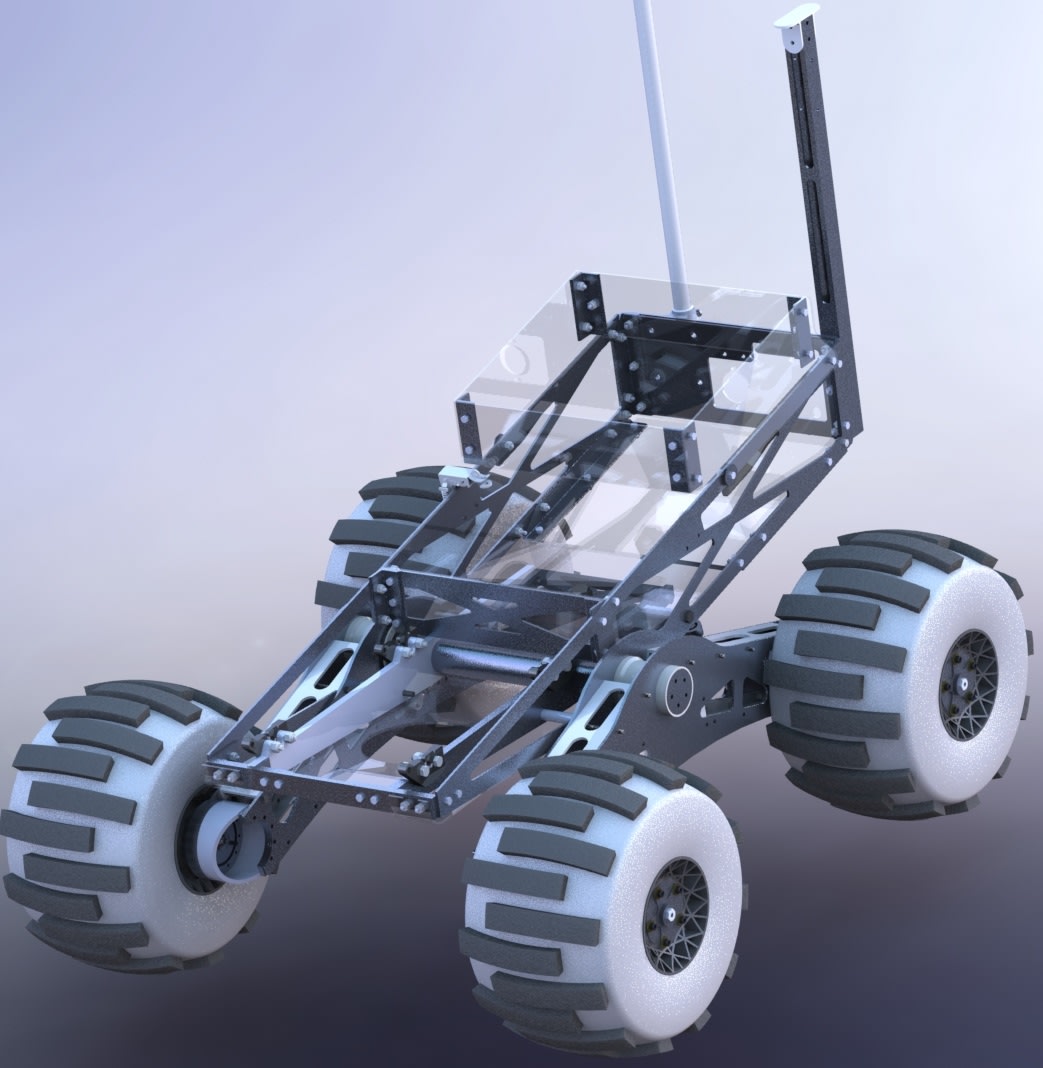
Specifically, your donation will support all of the following 5 subsystems, manufacturing team, and business operations team that comprise Husky Robotics:
- Arm: The Arm subsystem is responsible for the design, and construction of the rover’s robotic arm. The arm must safely lift to 5 kg, and needs to be dexterous enough to pick up tools, as well as perform complicated actions on a control panel and keyboard. Members of this subsystem learn to design in Autodesk Inventor Pro, use the machine shop to manufacture parts, and perform maintenance and repairs. This year Arm plans reiterate upon past functional designs such as by taking off weight, augmenting strength, and adding more cameras.
- Business: The Business team oversees fundraising, managing funds, seeking sponsorships, ordering parts, and making travel arrangements for the team to get to competition. The team also takes pictures, creates content for the web, and presents Husky Robotics Team to the UW, businesses, donors, and outside organizations. The business team emphasizes management of people, finances, and public profile, and works to provide opportunities to club members to develop valuable skills and find internships.
- Chassis: The Chassis subsystem creates a robust drive train to travel over the rough terrain of the competition while providing stable mounting points for the arm and science station. The group works with Computer Aided Design (CAD) software to create digital renderings and drawings of the rover, so the Manufacturing team can turn it into reality. During fall quarter, the chassis team works to fully design the base of the rover. Winter quarter, many Chassis members go into the shop to assist with manufacturing. In spring, the focus of Chassis turns to assembly and fixing any emergent issues.
- Electrical: The Electrical subsystem designs the architecture of electrical hardware that controls motors and interprets on the rover. It also designs the power distribution system and writes code to interface with electronics. Typical work for an Electrical member includes using Altium electrical CAD to create printed circuit boards, soldering, and testing motor control schemes.
- Science: The Science subsystem is responsible for designing and building the Science Station, a module on the rover that collects and analyzes soil samples, providing information such as soil temperature and water content. The subsystem also chooses and develops a set of off-rover soil tests, such as X-ray spectrometry, and provides background information to contextualize any findings during the competition. To successfully design the science station, the group leverages the University of Washington’s resources to get expert opinions and help from professors and graduate students.
- Software: The Software subsystem creates the “brains” of the rover, allowing it to be operated when it is out of sight of the driver. The group works with, computer vision, autonomous drive algorithms, inverse kinematics, as well as interfacing with different controllers to make sure the rover operates quickly and intuitively for the driver. The software team also creates the user interfaces that the drivers use to control the rover including camera feeds, on screen controls for precision based operations such as working with the science system, and map based coordinate plotting. Software uses the C++ programming language, Visual Studio, and Linux to achieve its objectives. Last year, Software began using mini-rovers to testbed controls and train members in programming on BeagleBone Black hardware.
- Manufacturing: Husky Robotics Team utilizes advanced manufacturing techniques such as CNC milling and lathing to create custom parts for the rover. Manufacturing also offers members a diverse skillset which includes welding, laser cutting, water-jetting, drilling, tapping, assembling, and 3D-printing. Manufacturing is highly involved with various types of materials such as aluminum, steel, plastics, carbon fiber, and bronze. Members are also personally trained by professionals and student experts to use machines safely and efficiently.
$25
Desktop Wallpapers
Every dollar counts! Get a folder packed with pictures of our rovers from this year and years past.
$75
Thank You Letter
$75 can go a long way. We'd like to thank you with a heart-felt letter and images signed by members of our team! (Includes all previous perks | Fair market value: $1)
$200
T-Shirt
Get a copy of this year's Husky Robotics t-shirt! (Includes all previous perks | Fair market value: $25)
$500
Rover and T-Shirt Recognition
You're out of this world! Get your name or logo featured on this year's rover, banners, and on the Husky Robotics website. (Includes all previous perks | Fair market value: $25)